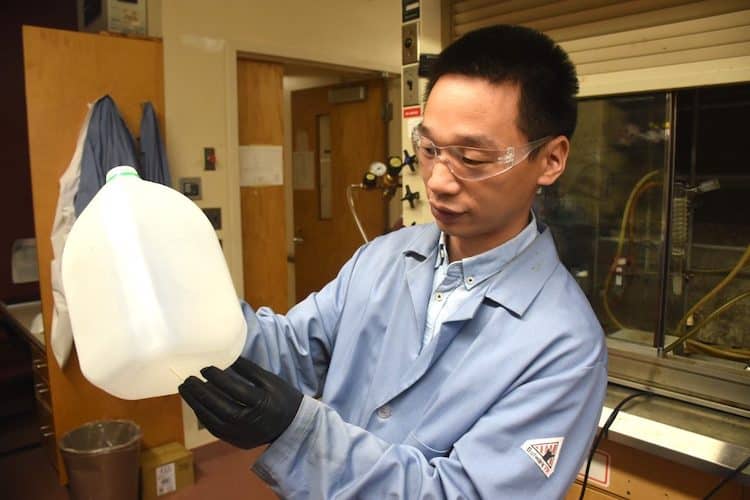
Guoliang “Greg” Liu in his lab. (Photo: Steven Mackay/Virginia Tech.)
Plastics are produced and used by humans like almost no other product. The material infamously lasts ages in landfills. This plastic waste problem is one of the largest environmental hurdles we face. Innovative solutions have been sought, but many require special chemicals or even worms to process plastic waste. Scientists from Virginia Tech have recently discovered a novel approach, announced in Science, that uses simple heat to convert polyethylene into the fatty acids that are the basis of soap, detergent, and other valuable products.
Polyethylene makes up most modern consumer plastics. Guoliang “Greg” Liu, an associate professor at Virginia Tech, noticed that their long carbon chain structure is relatively similar to fatty acids. The latter are carbon chains with a cluster of atoms at one tail. But how to convert one to the other? Liu took his inspiration from fire, which transforms wood into smoke. “Firewood is mostly made of polymers such as cellulose. The combustion of firewood breaks these polymers into short chains, and then into small gaseous molecules before full oxidation to carbon dioxide,” he explained in a statement. “If we similarly break down the synthetic polyethylene molecules but stop the process before they break all the way down to small gaseous molecules, then we should obtain short-chain, polyethylene-like molecules.”
Working with his graduate students Zhen Xu and Eric Munyaneza, Liu and his lab created a boiler system. Plastic—such as that found in plastic bottles—could be heated in an oven-like reactor. High temperatures lower in the container break the polymer plastic chains, while cooler temperatures slow this degradation as they migrate upwards. The wax, short-chain polyethylene, can then be removed from the reactor. Known as surfactants, this material is used in soaps and detergents. With a simple few more steps, it transforms into these high-value products.
There are many benefits to this new method of upcycling plastics. For one, it can be used with another type of common plastic, polypropylene. This eliminates the need to sort plastics by type. Additionally, it lacks the enzymes, worms, and other complex setups of other schemes. Lastly, soap and similar products are in high demand, so this process of reducing plastics to fatty acids may prove economically viable and encourage investment. The researchers responsible for this new process have high hopes.
“It should be realized that plastic pollution is a global challenge rather than a problem of a few mainstream countries. Compared to a sophisticated process and complex catalyst or reagent, a simple process may be more accessible to many other countries worldwide,” Xu said. “I hope this can be a good start for the war fighting plastic pollution.”
Researcher Guoliang “Greg” Liu created a boiler system to break down plastics into fatty acids usable to make soap.
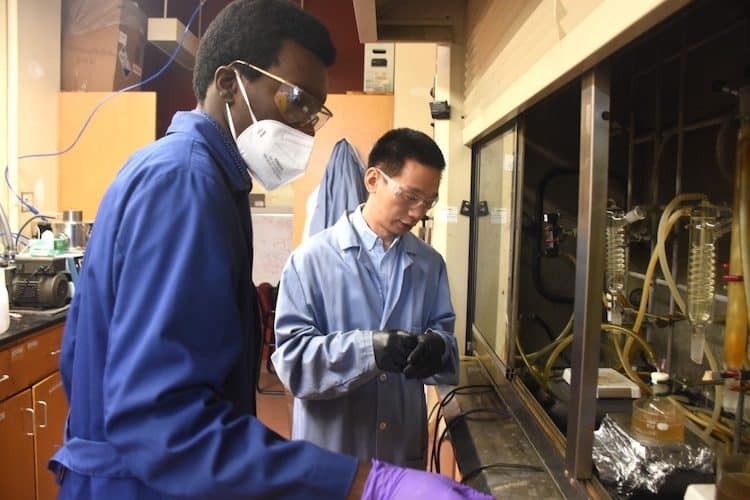
Liu and Eric Munyaneza preparing plastics. (Photo: Steven Mackay/Virginia Tech.)
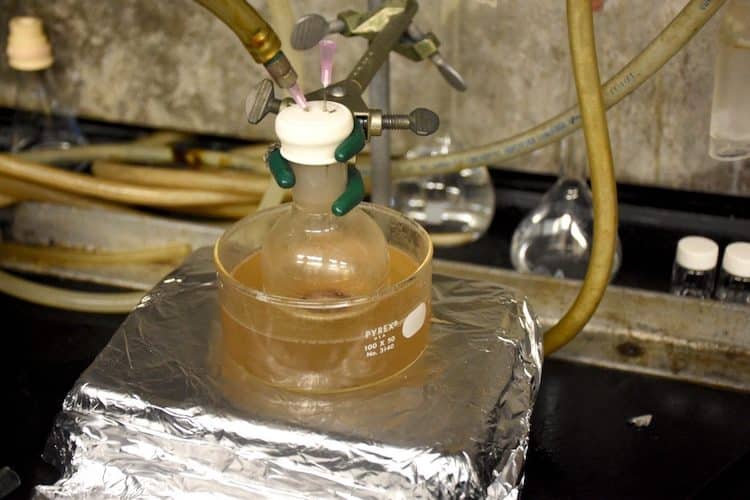
Wwaxes from polyethylene and polypropylene are heated to be oxidized to produce fatty acids via catalytic oxidation. (Photo: Steven Mackay/Virginia Tech.)
h/t: [Good News Network]
Related Articles:
Engineers Develop Enzyme That Can Break Down Plastic in a Matter of Hours
Scientists Discover Fungi That Can Eat Plastic in Just 140 Days
Ocean Cleanup Has Removed Over 220 Tons of Plastic Out of the Pacific Ocean
Student Designs 3D-Printed Robot Fish That Filters Microplastics From Water